Facility and Equipment
We make use of two CO2 laser cutting machines supplied by Mitsubishi. These high precision laser cutters perform with an accuracy within ±0.05mm.
Thanks to their high-level performance, the laser cutters can be used to process components for high-precision equipment such as banking ATMs.
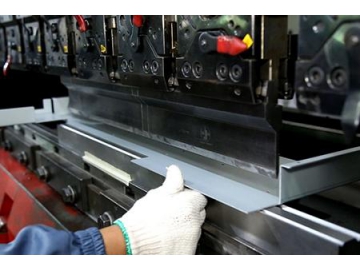
As for bending, we utilize both large-scale and small-scale bending machines to maximize our processing flexibility. This equipment is supplied by TOYOKOKI and Amada.
The length of products that can be bent by these machines is up to 3m with thickness ranging from 0.1-6mm.
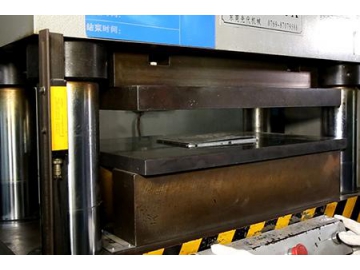
When customers submit special requirements in their drawings such as embossing and rib reinforcements, the traditional processing method involves creating expensive and time intensive custom stamping molds. We save time and money without sacrificing quality by using simple molds first and then cutting a template with a laser cutter before finally forming the workpiece with a hydraulic machine.
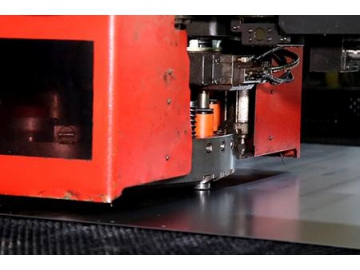
The Jiatong fabrication facility is equipped with Amada CNC punching presses to punch shapes out of sheet metal workpieces of all shapes, sizes, and purposes. This high-performance equipment is capable of punching 5 times per second and can ensure the precision of the hole and hole position with a margin of error of ±0.03mm and ±0.1mm respectively
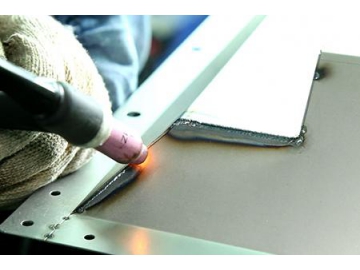
We are capable of performing high-precision welds using various methods. For example, TIG welding can handle the welding of refracting and oxidizing metals. MIG welding is most commonly applied for non-deformable products, and resistance welders are used to perform high-efficiency spot welding with neat and stable solder joints.
Surface treatments are processes applied after metal fabrication is complete. These treatments are used to give our products a more aesthetically pleasing appearance and also lengthen the product’s lifetime by protecting the components from the environment.
Some of the surface treatments we use include polishing, shot blasting, powder coating, screen printing, electroplating, anodizing, and laser marking. We are equipped with a complete semi-automatic electrostatic coating line. We even purchased a Gema electrostatic spray gun for flexible application to optimize the quality of custom products that are complex in shape.
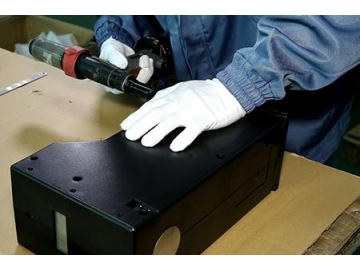
After the individual pieces of sheet metal have been processed through cutting, bending, stamping, welding, etc., we will then assemble them prior to packaging.
We carry out different forms of assembly such as:
Mechanical assembly: the customized sheet metal parts are assembled to the chassis or bracket by mechanical fixing methods using fasteners like rivets and screws.
Welding assembly: the customized sheet metal parts are assembled by welding such as TIG welding and resistance welding.