Twin Barrel
- High chromium cast iron Ω101A oval liner used for mixing of normal polymetric material.
- High vanadium cast iron Ω102A oval liner used for high proportion glass fiber reinforcement.
- Twin barrel with nickel based alloy bimetallic oval liner used to manufacture in corrosive conditions.
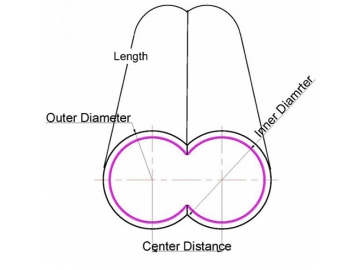
In the bimetallic C shaped lines, a common alloy layer is a boride cast iron with an excellent wear resistant performance. This alloy layer is Ω101, and is widely used in the twin extruder for modification markets.
ToIn comparison with an oval shaped liner, the two C shaped docking assembly is easy to make and install, leading to lower costs. However, this particular liner type features a few disadvantages, meaning the C shaped docking assembly cannot be used in a situation where the screw speed and back pressure are higher, as well as in situations where the polymer modification has higher physical performance requirements.
One piece of an Oval Liner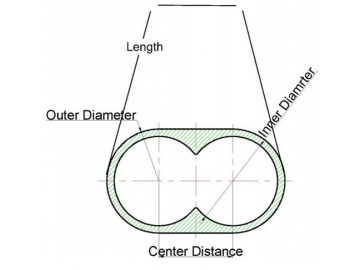
- These is no joint gap due to the use of only a single piece. This ensures users do not need to worry about any polymer material falling into gaps, and there are no dead areas inside the barrel. This guarantees that there is no risk of material contamination, and ensures an excellent self-cleaning performance.
- Stress inside the two acute angles after two C shaped liners are docked is avoided, reducing any risk of cracking inside the brittle iron base alloy layer.
- Even though there is a need for more torque, a higher screw speed, and a higher back working pressure in a high end parallel twin screw extruder, users do not need to worry about any liner rotation or displacement such as what often occurs when two C shaped liners are used.
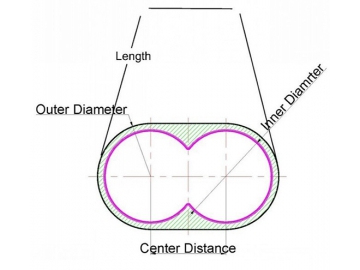
Inside two oval liner bores, there is an alloy protection layer, which is generally cast in two ways: one is an ordinary sintering process, and the other is the use of powder metallurgy high temperature molding by way of a PM-HIP static pressure.
The alloy clad layer of the bimetallic oval liner is usually made of a nickel-based alloy or cobalt-based alloy, and we can also add WC particles to improve the abrasive resistance of our products.
W6M5Cr4V2(M2) (The meterial type is high speed steel)
C12MoV(D2) (The meterial type is die steel)
Our company imported high-end CNC numerical control equipment used for the production of oval liners. Not only has this improved the cutting efficiency, but it has also improved liner manufacturing precision in a number of areas.
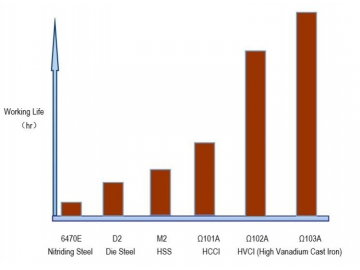
The above data is based on the test results provided by Material Test Center of Chinese Mechanical Industry(MTCCMI) and Test Center of Shanghai Material Research Institute(TCMSRI), the time is April 2014, on the same conditions of friction wheel, friction line speed and friction charge.
“Ω” Series alloy is researched and developped by us for inquiries of Germany W&P Company, specially to be designed to the Parallel Co-rotating Twin Screw Extruder combination barrel. Ω101A is the same as code name 043 of W&P Company, Ω103A is the same as the code name 99.3 of W&P Company, the wear-resistant ability of Ω102A is a little worse than Ω103A but with more cost-effective. Normally these two kinds of HVCI alloy oval liners are used on the feeding section for high percentage of GF reinforced due to they higher wear resistance than normal steel oval liner.